EcoFlow Delta PRO deep-dive review
_CONECTIVITY – APP – FW UPDATE_
The DeltaPRO can only connect to 2.4Ghz wifi networks so I advise everyone to first connect your phone to the 2.4Ghz wifi network that you’re going to connect the DeltaPRO to and follow the instructions.
Once the DeltaPRO connects correctly, you can go back to your usual WIFI network.
In my case I used an iPhone 11 ProMax running iOS 14.3 (JB) with Ecoflow app version 2.5.3.12 and the setup went without any problems.
The app, which has seen multiple iterations over the course of two months, is clean and intuitive.
I want to thank the app/software team at Ecoflow and ask them to keep improving & adding features like data recording for us nerds.
I’d also wish they would expand on the parameters that we can control in the settings tab and maybe add the option to program the DeltaPRO to charge from AC on a set period of time like off-peak; I know you can do that with the Smart Home Panel but for those who don’t have it, it would be a welcome feature.
The FW update from 0.1.0.0 to 1.0.0.60 over WIFI took around 12 minutes and went without a hitch. I recommend you unplug all cables connected to the DeltaPRO as it is going to turn on/off multiple times while it is upgrading the FW of the various internal components.
Once all is done you should go back to the app and check that everything is working correctly.
If you have connectivity issues or the app is behaving in a weird way, I recommend you completely uninstall the app and reinstall, login with your credentials and test again.
NOTE: I’ve recorded the whole process when I went from .60 to .68 so you can see what to expect.
NOTE2: I’m currently testing FW .71 and will report back my findings soon. Sadly I have the same exact issues as in previous versions… 🙁
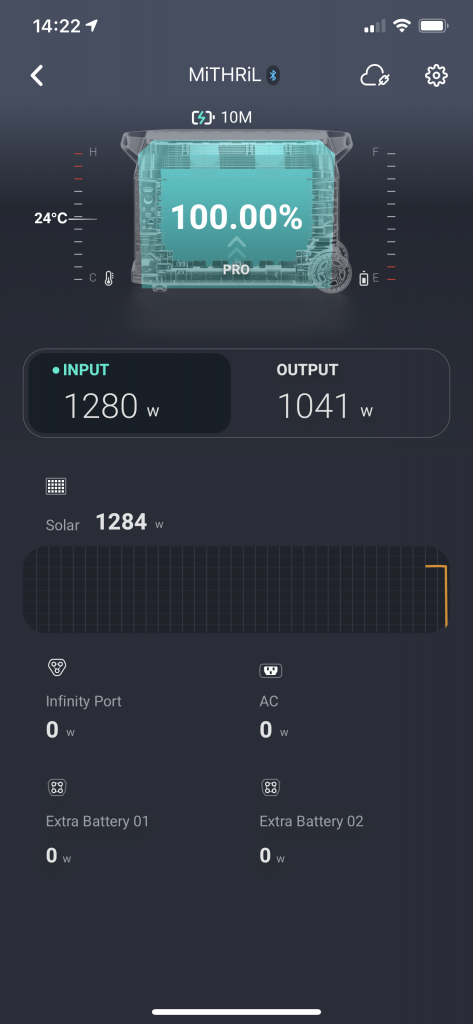
Next I configured the DeltaPRO to my liking and set an 800W AC charging speed and let it charge to 100% with everything turned off (so no AC/DC/USB). Once the unit reached 100% I unplugged it and turned it off (LCD showed “0000 OFF”) to let the BMS slowly rebalance the individual cells of the battery.
Initially when I received my DeltaPRO the app was excruciatingly slow over 4G and sometimes would even time out as it was trying to communicate with a single overloaded server located in China but I’m happy to report that Ecoflow engineers have since upgraded and greatly improved the speed.
I immediately noticed the difference when using my own program with reply times dropping from 30s+ to as low as 0.5s so congratz to them for reacting fast and fixing the problem! 🙂
The next day I did a full drain test with a 900W space heater that got me as close as possible to PF=1 (power factor) to check the external AC usable watts/runtime (not to be confused with DC internal battery capacity). Once I reached 5% battery, I lowered the space heater to 450W to reduce the discharge rate so as to avoid any of the battery cells dipping below cutoff voltage. The app showed “05 M” for more than an hour before the inverter automatically turned off and the unit went into “Standby” mode. The temperature reported by the app went from 21c to 26c with about 2.900W AC and 4 hours of runtime.
DeltaPRO Data Insight
The results were OK for an initial test but I immediately realized that this kind of “outside” testing yielded poor/coarse data so I decided to poke inside the DeltaPRO (software side) and ended up writing a quick Python program to extract all the juicy data that the DeltaPRO produces every second ^-^.
From this point on, all claims are based on numbers obtained directly from the DeltaPRO with some extra external data where useful to compare or complement.
I want to stress that my calculations are based on how many watts I manage to put into the battery and how many watts I take out of the battery.
Operational costs in Watts (Battery DC)
- DP ON | LCD ON | FAN OFF | INVERTER OFF = -6W/h to -12W/h
- DP ON | LCD ON | FAN OFF | INVERTER ON + NO LOAD = -43W/h to -51W/h
- DP ON | LCD ON | FAN ON | INVERTER OFF | MPPT ON = -13W/h + 75% to 98% conversion efficiency.
- DP ON | LCD ON | FAN ON | INVERTER OFF | AC CHARGING = 72% to 90% conversion efficiency.
- Most efficient AC charge speed is 1.800W at 89,80% (0.5C).
- AC INVERTER efficiency for a PF=1 load of 450W is around 95%
- AC PASSTHROUGH seems to burn around 20W/h
- I presume there are 30 battery cells distributed in a 15S2P (need confirmation) for a total of 80A at 48V which gives a design capacity of 3.840W.
- Highest recorded pack voltage = 51.55V
- Highest recorded pack voltage while charging = 52.80V
- Lowest recorded pack voltage = 45.50V
- Highest recorded battery capacity = 3.684W (10D15H)
- Highest cell-level balance efficiency = 99.80%
- Lowest cell-level balance efficiency = 94%
- Highest MPPT controller IN Amps = 15.99A
- Highest cell-level temperature difference = 3c
- Highest MPPT controller recorded IN Watts = 1.619W
- MPPT conversion efficiency at 1.6KW around 95%
- MPPT conversion efficiency at 100W <= 75%
- Highest MPPT controller reported temperature = 104c (Fan State = 3)
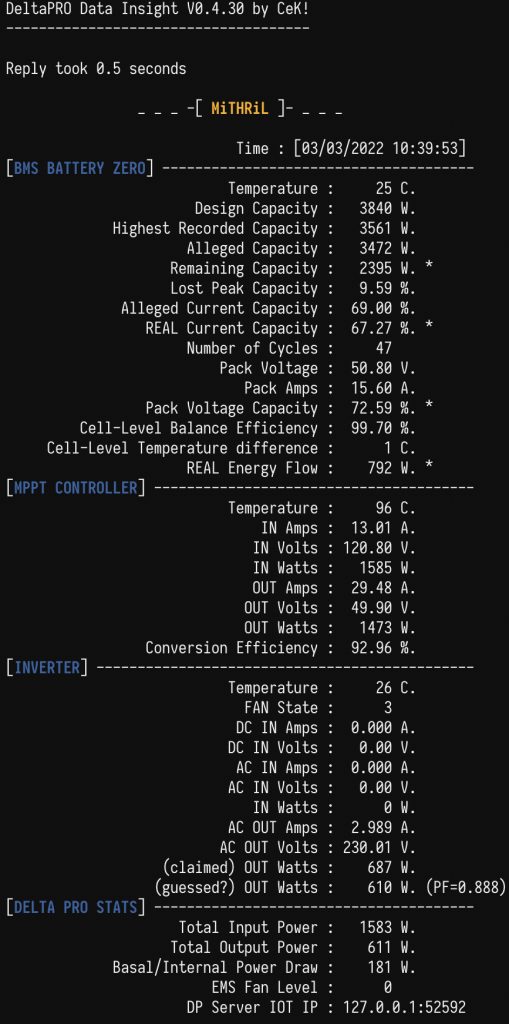
_DeltaPRO General_
One nice thing about the DeltaPRO’s LCD is that it reports time left % and input/output watts in a very simple and clean way but sadly, for the time being (FW .68/.71), the watt output readings are never correct and get more inaccurate the farther your are from the ideal PF=1 (Power Factor).
As for the time left %, most of the time, it is not accurate at all and depends on the BMS’s calculations of what it thinks is left in the battery pack.
Firstly this inaccuracy is due to the fact that the LFP chemistry used in the DeltaPRO’s battery pack has a very flat voltage discharge curve that makes it hard for the BMS to guesstimate the remaining capacity so with repeated shallow charge/discharge cycles the estimate error will accumulate up to a point where I was powering 150W+ AC load for more than 3 hours with 1% battery capacity.
In a healthy DeltaPRO this happens because of an imbalanced battery pack where one cell is above or below voltage compared to the rest of the cells and the BMS wasn’t able to balance them correctly. The only way (at the time of this writing) to help the BMS correct it’s precision drift is to do an uninterrupted deep discharge/charge cycle as follows:
- Discharge the DeltaPRO as you would normally do up until you get to around 2-3% remaining capacity.
- Lower your discharge rate to < 100W (50W even better) up until the AC inverter turns off; this is to be as gentle as possible so the voltage of each individual cell of the battery pack will be as close to each other as possible. Any single cell that dips below cut-off voltage will trigger the disconnection so we aim to avoid that with a very low discharge rate to distribute the load on each cell as gently as possible.
- Once the AC inverter has turned off, wait 5 minutes and start recharging the battery again, preferably with a 0.5C (1.800W) or lower charge rate.
DO NOT UNDER ANY CICRUMSTANCE leave the DeltaPRO in that discharged state for a long period of time or you will risk the battery entering “hibernation” mode to protect itself. - Once you reach 98% of charged state, lower charging rate to 200W so as to not trigger a cell to go above cut-off voltage; you want to be as gentle as possible so all the cells have the same voltage.
- You will notice that it might stay in 99.49% (for FW .68|FW .71 seems to have corrected this and now goes all the way to 99.99%) & something like 10M left to complete for a long time; totally normal and expected.
- Once it stops charging, you have reached full capacity and have helped the BMS recalibrate the capacity it thinks is available.
In my specific use case, I went from a mediocre 2.980W to 3.684W as reported by the BMS.
It seems that (FW .71) the maximum capacity you can reach is 3.684W so I presume the rest up to 3.840W is saved as extra capacity to protect the DeltaPRO when it automatically disconnects the AC inverter and goes into standby mode.
I advise owners to invest 10€ in a single outlet surge protector to protect your DeltaPRO if you usually leave it plugged on AC/AC pass-through.
Some people over FB reported that their DeltaPROs got the dreaded “magic smoke” caused by what I presume was a burnt AC inverter as they couldn’t turn on the AC inverter nor charge their DeltaPROs with AC wall plug but DC was still working.
The DeltaPRO fans are very powerful so they will be noisy and pull dust, a lot of dust, no matter how clean the environment is so keep that in mind and maybe clean the intake once a week.
I have a feeling that in due time I’ll have to take apart the (top of the) DeltaPRO to clean all the accumulated dust just like I would do for any of my pc/servers/laptops.
Be very mindful to not cover/obstruct the intake/exhaust fans as it could lead to overheating & shutdown.
Once you turn off the DeltaPRO (press & hold power button for 3 seconds) you will only be able to remotely power it back on if you’re in range of BT. 4G will never work as DeltaPRO’s wifi will be turned off (disconnected from the internet).
One trick that I use (if I would ever need) to remotely power on my DeltaPRO when I’m outside the house is to turn on the smart plug that feeds the DeltaPRO. Once the DeltaPRO senses AC wall current it will power on automatically and after a minute or so you’ll be able to control your DeltaPRO from the app over 4G.
Hi, very nice review I am interested.
When will you post the extra-battery review?
Hi Jo.
I currently don’t have the Ecoflow DeltaPRO Smart Extra Battery so I can’t test it 🙁 … but do keep an eye at this review for updates and maybe in the near future I’ll be able to test it.
Thank you for your time and comment.
I am interestet but I will wait when you post that device bugs are fixed.
Hi Locutus,
I’m sure Ecoflow will fix these issues fast!
I’ll update this post with all my findings and strike all bugs when they will be fixed.
Thank you for your time and comment.
Very nice review, thanks. I’m interested in how you wired the Ecoflow to the Transfer Switch and your electrical grid – will you write an article about that topic? I think a lot of European users would be interested in a detailed description with pictures. Looks really amazing so far! Best wishes
Hi Ralf,
This is part of a series of articles for the Spanish market where there’s a lot of interest for this kind of “easy” DIY solutions.
I will be writing about my detailed setup with the ATS and solar panels in an upcoming article.
Stay tuned! 🙂
Thank you for your time and comment.
Thanks, I’ll definitely stay tuned. In Germany, the Netherlands and Denmark the interest for diy solutions is also pretty high, even though we don’t have so much Sun as you guys in Spain. Looking forward to read more of your articles, best wishes!
Yeah we are spoiled here 🙂
Thanks for the wishes and likewise!
Thank you for such detailed review. Would you mind sharing the script you have to pull the data from the DeltaPRO ? Many thanks
Hi, you’re most welcome!
I’ll share it once I have the time to clean it up and put it on github with proper instructions.
Thank you for your time and comment.
This is super amazing. I’ve been dying to get data _out_ of my DP, but the best I’ve got is the puny REST API. Can you pull back the curtain on how you’re pulling these DP values into software?
Hi Scott; thank you for your time and comment and apologies for the delay in replying.
I’ve been asked by Ecoflow not to release my program or related information…
Maybe if we all keep asking Ecoflow to release a proper API and/or a service so we can automate everything around the DeltaPRO that is easy enough so anyone can make use of it they will end up hearing us and implementing it?
Pingback: DeltaPRO Firmware 1.0.0.74 Review – DringLord
I too have just suffered an exploding Delta Pro. It was in pass through mode and just went BANG with smoke issuing from the fan grilles. Firmware version was 0.3.6. I don’t know where version “85” or “89” went to!
Awaiting a response from Ecoflow.
Have you noticed MPPT charging stopping if you over power the input? was trying to maximize solar charging input and I am afraid I may have friend the MPPT. Is there a way to reset the MPPT? or does anyone have schematics so I can take it apart and fix it? thank you so much!
Ouch! Hopefully it turns out to be nothing!
First thing I can say is to NOT OPEN the DP yourself but to go to the FB forum and ask for help from an EF employees.
I never went above 147V (VOC) even with +5C in winter so I personally don’t know what would happen if you get above it and actually don’t want to find out…
Let’s go back to basics, step by step:
The easiest thing to do is to try to smell for burnt electronics (very pungent so for sure you would smell it).
Select only ONE PV panel, hook it to the MC4 cable that came with the DP (do not connect the cable to the DP) and user tester to see if you get a voltage reading from it.
If you get a voltage reading from the one panel, you can connect it to the DP and check if there’s a small voltage drop (example: unhooked 20V, hooked:18V).
If you have a voltage drop, try to connect and disconnect at least 4 times the panel from the DP (Nothing else connected to the DP, no input or output).
Also make sure you haven’t set any charging/discharging limits: it should be 0% to 100%.
In the most recent FW, from my testing it seems they’ve introduced a counter where the MPPT controller would not engage until the fourth connect/disconnect, especially when the DP is near full.
Also do not design your PV array to go above 125V when under full load or you would hit the internal limiter and stay at 1.285W (and your internal temps will shoot very high).
To reset the onboard ESP-M (computer) you have to disconnect everything from the DP, hold the power button (big gold round button) for 15 seconds. You should see “OFF” on the LCD for a brief moment but keep holding that button until you count 15 seconds.
Once done, hold the same button for one second and let go. If you don’t see the WIFI icon when the LCD lights up it means that you succeeded in resetting the computer. Among other things, it will reset the fuel-gauge.
Let us know how it goes and again, DO NOT OPEN THE DP! (and ask for help over FB)
Brilliant review! Thank you.
Can you share details of your improved cooling solution? I am afraid the noise from the stock version is a deal breaker for me.
Also, what made you choose the Ecoflow delta pro over the Bluetti ac300/B300?
Thank you and cheers from Denmark🙏
Hi Nikolaj & thank you for your comment.
If you check the comments section of the youtube video you will have a rough idea of what I did.
I chose EF because I managed to get a unit for 1.999$ (Super Early Bird) which was a great price and to me it looked nicer and more well rounded but of course I would have loved to check the Bluetti brand and compare them.
Have a great week!
Pingback: EcoFlow Delta PRO 6+ months review – DringLord